Voix de l’industrie : l’IIoT prolonge la durée de vie utile des équipements hérités
À mesure que les capacités de l’Internet industriel des objets (IIoT) se développent, les fabricants tireront davantage parti de leurs systèmes existants.
Les contraintes de la chaîne d’approvisionnement et une forte augmentation de la demande ont poussé les exploitants d’usines et les fabricants à trouver des moyens d’améliorer la productivité de leurs équipements. Le principal défi de ces améliorations consiste à extraire davantage de données de l’équipement, afin que les opérateurs puissent apporter des modifications significatives et éclairées.
Des entreprises comme Banner Engineering ont trouvé des moyens d’aider les entreprises à tirer parti de l’IIoT sur leurs équipements hérités. Souvent, cet équipement hérité est en excellent état et fait bien son travail, il n’est donc pas nécessaire de tout réviser. Il existe plusieurs stratégies à faible risque pour mettre à niveau cet équipement afin d’obtenir les performances et la disponibilité dont vous avez besoin.
Nous avons rencontré Luke Karnas, directeur du développement commercial, IoT, chez Banner Engineering, pour nous donner des détails sur l’utilisation de l’IIoT pour améliorer l’utilité et les résultats des équipements existants.
Design News : Pourquoi est-il si important pour les exploitants d’usines de comprendre les capacités de l’IIoT sur les équipements hérités ?
Luc Karnas : Il y a tellement d’équipements qu’il n’est pas nécessaire de remplacer ou de réviser complètement l’équipement juste pour commencer à le surveiller.
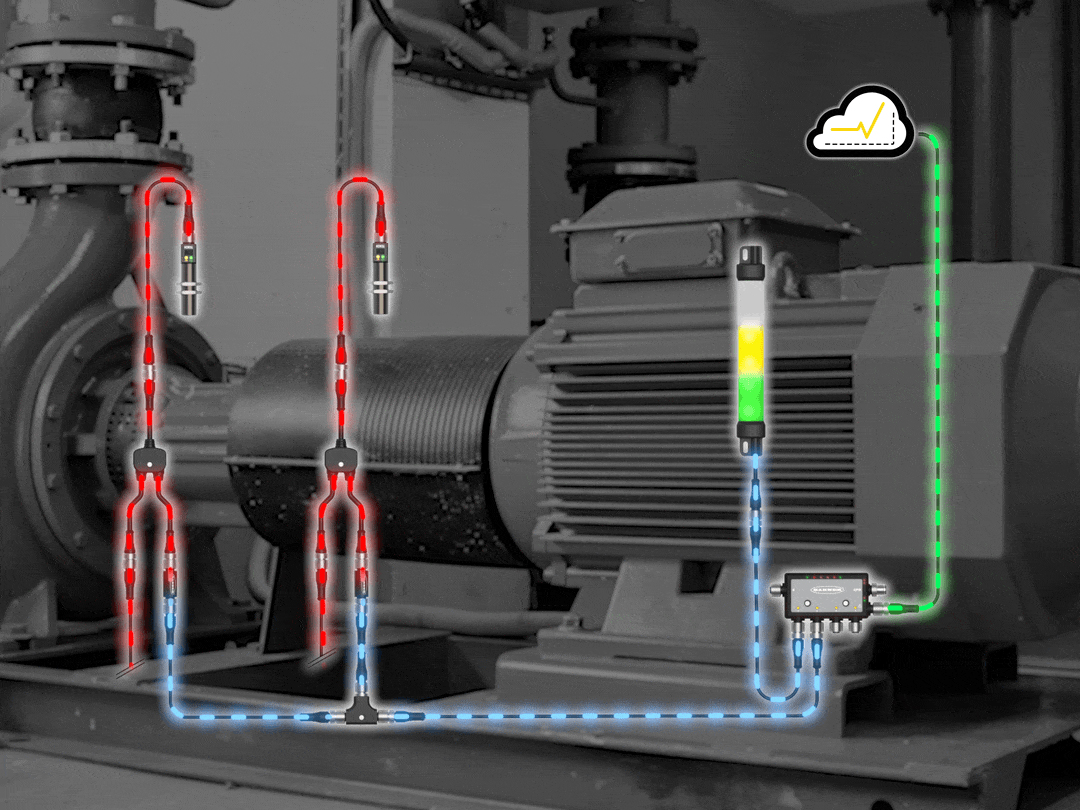
Ce schéma montre un système IIoT mesurant la température.
DN : Pourquoi un directeur d’usine serait-il intéressé par la surveillance d’un équipement ?
Luc Karnas : Vous ne pouvez pas gérer ce que vous ne mesurez pas. La plupart des équipements industriels contiennent des données précieuses, notamment des capteurs qui pourraient effectuer un autre travail, mais qui pourraient être surveillés et transformés en données de productivité.
DN : Quels ont été les défis pour accéder à ces données dans le passé ?
Luc Karnas : La plupart des approches reposent sur l’accès à l’automate de la machine, mais la plupart des équipementiers n’autorisent pas les utilisateurs à ajouter ou à modifier du code sur leur équipement. De plus, les clients finaux peuvent ou non avoir les compétences nécessaires pour le faire par eux-mêmes. Snap Signal nous permet de surveiller l’équipement sans nous impliquer dans le contrôle.
Voici un schéma d’un système IIoT qui surveille les niveaux des réservoirs.
DN : Pour les utilisateurs finaux, quelles sont les équipes qui bénéficieront le plus de l’IIoT ?
Luc Karnas : Une fois que vous avez les données, il est étonnant de voir combien de personnes peuvent bénéficier des nouvelles informations. Le personnel de maintenance peut surveiller l’équipement 24 heures sur 24 une fois qu’il est équipé de capteurs de surveillance de l’état, et peut anticiper la maintenance ou les pannes avant qu’elles ne surviennent. Les ingénieurs en amélioration des processus pourront voir les performances de lignes de production similaires jusqu’au niveau de la machine pour comprendre où existent les contraintes afin que des modifications puissent être apportées pour les éliminer.
Les ingénieurs qualité seront en mesure de suivre les taux de rebut et d’exécution pour s’assurer que les problèmes sont résolus rapidement, réduisant ainsi les déchets et les coûts qui en découlent. Les directeurs d’usine seront en mesure de mieux comprendre la capacité totale, ce qui leur permettra de mieux planifier et d’offrir des prévisions plus précises aux autres parties prenantes de l’entreprise.
DN : Comment Banner est-il positionné pour aider les fabricants avec l’IIoT ?
Luc Karnas : Nous avons adopté une approche différente, plus complète, ce qui signifie que nous offrons tout, des capteurs pour recueillir de nouvelles données, des produits pour récolter les données existantes, des contrôleurs et des tableaux de bord pour les surveiller. Nous visons à réduire la complexité en réduisant la charge de l’utilisateur final en consolidant l’ensemble de la pile technologique et l’effort de mise en œuvre.