Les systèmes de convoyage et de transport automatisés offrent une nouvelle flexibilité dans la fabrication de dispositifs médicaux
Tenez compte de ces 5 facteurs lors de l’évaluation de la dernière génération de convoyeurs intelligents pour la fabrication de dispositifs médicaux.
Dans la fabrication de dispositifs médicaux, les entreprises doivent tirer parti de toutes les opportunités possibles pour augmenter la productivité et le débit, réduire les coûts, éliminer les déchets et améliorer la qualité et la fiabilité des produits, tout en gérant le changement au quotidien. Il existe un certain nombre de technologies de production et d’assemblage dotées de nouvelles capacités qui peuvent aider les fabricants de dispositifs médicaux à atteindre ces objectifs. L’un d’eux est les systèmes de convoyage automatisés. La mise en œuvre d’un convoyeur automatisé, en particulier dans les opérations d’assemblage ou d’emballage, peut augmenter la flexibilité et la productivité de la fabrication.
La dernière génération de convoyeurs et de systèmes de transport intègre des fonctionnalités qui peuvent permettre de nouveaux niveaux d’automatisation pour la fabrication de dispositifs médicaux. Le choix de la bonne méthode de transport et de convoyage automatique est souvent déterminé par le flux de matériaux, le volume de production et la gamme de produits.
Sommaire
Défis de la fabrication de dispositifs médicaux
Les produits créés par les fabricants de dispositifs médicaux sont des dispositifs de grande valeur, souvent assez sophistiqués, utilisés par des millions de personnes pour des besoins vitaux de soins de santé à court et à long terme.
Ces produits et leurs procédés de fabrication ont tendance à être très réglementés, nécessitant une documentation complète et un contrôle qualité rigoureux de leurs opérations. De plus, les fabricants de produits médicaux sont confrontés à certaines des conditions de fonctionnement les plus exigeantes :
- Courtes séries de produits et réduction des cycles de vie des produits
- Produits complexes nécessitant un assemblage de précision en plusieurs étapes
- Petits composants sensibles qui doivent être manipulés avec délicatesse
- Propreté stricte et contrôles environnementaux
L’un des moyens par lesquels les fabricants de dispositifs médicaux, à l’instar d’autres fabricants leaders, résolvent ces défis est de mettre en œuvre des processus de fabrication sans gaspillage efficaces. La production au plus juste offre un moyen systématique d’identifier les déchets et de les éliminer.
Certains processus de fabrication ou d’assemblage de dispositifs médicaux fonctionnent mieux en utilisant des processus de production entièrement manuels, avec peu ou pas de systèmes automatisés de transfert ou de transport de matériaux nécessaires. Il s’agit de produits avec des quantités de production faibles ou incertaines, ou pour lesquels la demande pour différents produits est incertaine, de sorte que le mix de production a une faible prévisibilité.
Alors que la gamme de produits devient plus prévisible, avec des séries de produits plus longues pour répondre à une demande accrue, la production automatisée est le bon choix lorsqu’elle aide les fabricants de dispositifs médicaux à augmenter la fiabilité des processus et à réduire les coûts pour récupérer l’investissement dans le transport automatisé.
Dans le passé, l’utilisation de systèmes de convoyeurs dans des environnements de production au plus juste était souvent rejetée ; on pensait qu’ils étaient trop rigides et pouvaient potentiellement verrouiller des processus de production inefficaces en place, empêchant les efforts efficaces de rationalisation pour éliminer les déchets.
Les systèmes de convoyeurs flexibles d’aujourd’hui vont bien au-delà et contribuent à minimiser les déchets dans la production à faible mélange et à volume moyen à élevé que l’on trouve couramment dans de nombreuses applications de production de dispositifs médicaux. En combinant la vitesse avec un suivi intégré des pièces, un maintien précis des pièces et un positionnement de travail ergonomiquement correct, les systèmes de convoyeurs bien mis en œuvre sont un élément clé de l’usine au plus juste.
Choisir le bon type de convoyeur
Selon le type de dispositif médical produit, il existe une gamme de systèmes de convoyage standard utilisés dans ces opérations. Les systèmes de convoyage peuvent généralement être classés en fonction du type de support de convoyage qu’ils utilisent. Pour les fabricants de dispositifs médicaux, deux des systèmes les plus couramment utilisés sont les convoyeurs à double brin ou les convoyeurs à chaîne en plastique.
Ces systèmes peuvent transporter des charges de 10 kilogrammes ou plus, ce qui répond aux exigences d’un large éventail d’opérations de production de dispositifs médicaux et de kits médicaux. Les vitesses de transport typiques sont de 10 à 12 mètres par minute et utilisent des déviateurs pour décharger des produits ou des composants sur les postes de travail ou les systèmes d’assemblage.
La plupart des convoyeurs sont alimentés par des moteurs à courant alternatif tournant à une vitesse constante, se déplaçant dans une seule direction. Les produits sont transportés dans des bacs ou sur des palettes et sont livrés à des points de consigne sur toute la longueur du convoyeur par des butées ou déviateurs mécaniques ou pneumatiques.
Le suivi des produits sur le système implique souvent la fixation d’étiquettes RFID, soit directement sur le produit transporté, soit sur un sac, qui contient parfois plusieurs articles, ce qui complique le suivi. Il s’agit d’une préoccupation cruciale pour les fabricants de dispositifs médicaux soumis à des exigences réglementaires pour suivre et documenter la manière dont chaque composant de chaque dispositif a été manipulé, intégré et testé tout au long du processus de production.
Ces convoyeurs standard ont tendance à « verrouiller » la vitesse et le flux de fabrication, avec un débit déterminé par la limite supérieure du convoyeur. Si de nouveaux produits nécessitent l’ajout d’une station d’assemblage ou d’une machine supplémentaire dans le flux de production, la modification de la configuration du convoyeur peut entraîner des temps d’arrêt et des coûts d’ingénierie.
Alors que pour certaines opérations ce type de transport est suffisant, certains fabricants de dispositifs médicaux ont des besoins plus complexes : ils peuvent avoir besoin de déplacer les produits à travers différentes étapes d’assemblage beaucoup plus rapidement, ou ils peuvent avoir besoin de faire varier la vitesse, et dans certains cas la direction du mouvement. , pour répondre aux exigences de production uniques.
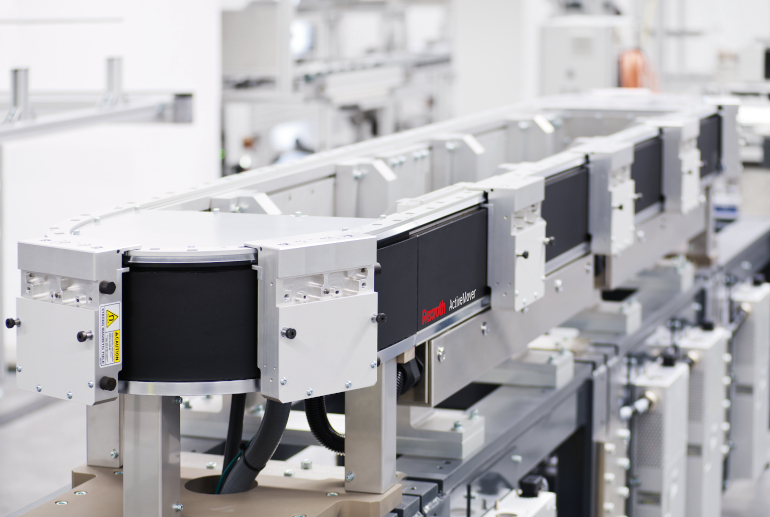
Le positionnement variable et flexible de chaque palette porte-pièces signifie que les fabricants d’appareils peuvent personnaliser le mouvement de chaque palette pour répondre aux exigences d’assemblage spécifiques au produit.
Nouvelle génération de systèmes de transport
De nouveaux systèmes de transport de matériaux sont désormais disponibles qui, dans une certaine mesure, redéfinissent les capacités et le potentiel des convoyeurs. L’un des avantages les plus importants qu’ils offrent est qu’ils sont conçus pour une plus grande flexibilité, précision, vitesse et contrôle des processus, des avantages que les fabricants de dispositifs médicaux peuvent utiliser pour augmenter la productivité et faciliter une production plus flexible en réponse aux demandes en constante évolution du marché.
Ces systèmes prennent également en charge un débit beaucoup plus rapide et une utilisation plus efficace de l’espace au sol de fabrication coûteux, et ils peuvent plus facilement suivre les activités de transport des matériaux et communiquer ces données aux systèmes de gestion de l’usine à des fins de documentation et d’analyse.
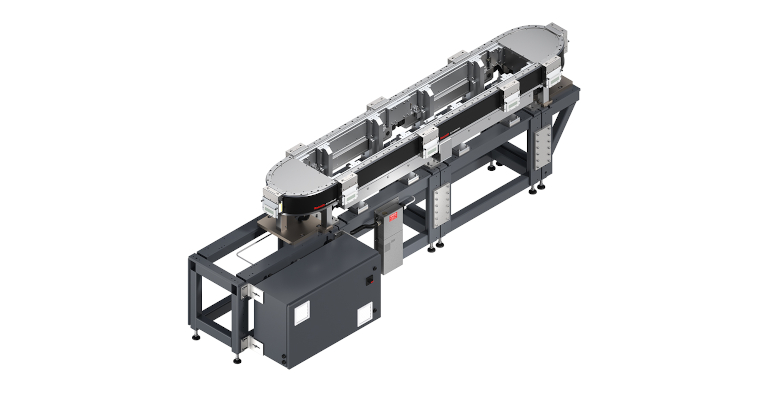
Les positions d’arrêt peuvent être configurées dans le logiciel n’importe où dans le système, même dans les courbes. Beaucoup disposent de systèmes de mesure intégrés qui permettent une indexation précise des palettes, éliminant le besoin d’unités de levage et de localisation supplémentaires.
Lors de l’évaluation de la dernière génération de convoyeurs intelligents à sélectionner, les fabricants de dispositifs médicaux doivent prendre en compte plusieurs facteurs lorsqu’ils choisissent la meilleure solution pour leurs besoins :
- Innovation. Un système innovant remplace entièrement la courroie ou la chaîne typique associée aux convoyeurs standard. Au lieu de cela, il utilise un moteur linéaire rotatif avec des palettes de pièces montées verticalement, le mouvement de chaque palette de pièces pouvant être défini individuellement – à quelle vitesse elle va, où elle s’arrête – et même pour inverser le mouvement. Ce type de mouvement flexible garantit que les fabricants bénéficient des principaux avantages du transport automatisé sans être enfermés dans certains de ses inconvénients.
- La vitesse. Les systèmes à moteur linéaire combinent un mouvement polyvalent avec des vitesses de transport allant jusqu’à 4 mètres par seconde, nettement plus rapides que de nombreux convoyeurs standard. De plus, certains systèmes présentent des temps de changement de palette porte-pièces inférieurs à une seconde. Et comme chaque palette est programmable indépendamment, sa position peut être suivie et documentée avec une précision de 100 %. Un débit plus rapide et un suivi serré au niveau des palettes peuvent augmenter la productivité, contribuant ainsi à réduire le temps de cycle et les coûts de fabrication.
- Précision. Ces nouveaux systèmes offrent également un nouveau niveau de précision de point final avec des points d’arrêt individuels hautement reproductibles de ± 0,01 millimètre. Les positions d’arrêt peuvent être configurées dans le logiciel n’importe où dans le système, même dans les courbes. Beaucoup disposent de systèmes de mesure intégrés qui permettent une indexation précise des palettes, éliminant le besoin d’unités de levage et de localisation supplémentaires. Ce positionnement variable et flexible de chaque palette porte-pièces signifie que les fabricants d’appareils peuvent personnaliser le mouvement de chaque palette pour répondre aux exigences d’assemblage spécifiques au produit. Le contrôle précis fourni par le moteur linéaire signifie également qu’il n’y a pratiquement aucune perte de temps pour positionner la palette devant chaque poste de travail.
- Conception robuste. Ces types de systèmes intègrent également de nombreuses fonctionnalités dans des encombrements réduits : certaines installations ont remplacé plusieurs convoyeurs par un seul système de transport linéaire et économisé près de 40 % de l’espace au sol de l’usine. Ils sont dotés d’un entraînement puissant avec jusqu’à 160 newtons par palette et intègrent des modules de courbe à 180 degrés et à 90 degrés pour permettre une variation accrue des dispositions du système de transport. De plus, les systèmes de transport comme ceux-ci prennent généralement en charge les interfaces de nombreux bus d’automatisation à grande vitesse, tels que ProfiNet et Ethernet IP, et EtherCAT. Ces interfaces permettent une intégration plus facile avec le réseau fédérateur de communications machine existant d’un fabricant d’appareils ainsi que la connexion à des appareils informatiques de pointe.
- Soutien technique. L’une des capacités essentielles à évaluer lors de la sélection des systèmes de transport par convoyeur est l’assistance technique et les capacités de simulation disponibles pour la conception du système et la programmation de ses opérations, avant même que le matériel n’entre en jeu.
Les utilisateurs doivent s’assurer que le simulateur permet la création d’un « jumeau numérique » de leur machine. Avec un, ils pourraient calculer la consommation d’énergie, déterminer le temps de cycle, le nombre de palettes et d’unités d’alimentation dont leur système aura besoin, et ils pourraient entièrement programmer le système, définir des séquences de mouvement, des positions d’arrêt, des configurations de déplacement et de nombreuses autres fonctions du système.
Ce type d’outils de simulation et de configuration pour l’utilisateur final peut permettre aux fabricants de dispositifs médicaux de mettre en œuvre les dernières technologies beaucoup plus facilement sans passer par des courbes d’apprentissage abruptes.
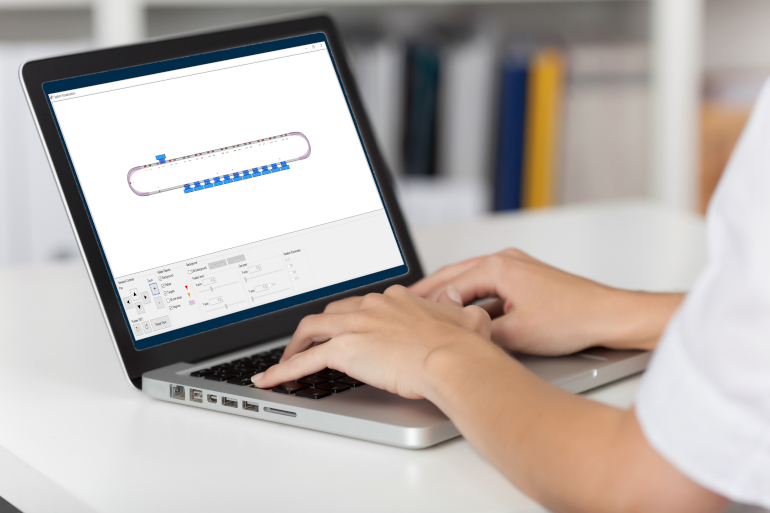
Avec le logiciel ActiveMover AMpro de Bosch Rexroth, les clients peuvent concevoir et construire leurs systèmes virtuellement avant de recevoir leur matériel, éliminant ainsi le temps de démarrage. L’ActiveMover virtuel peut s’interfacer avec presque tous les automates et répondra de la même manière que le système physique.
Alors que les fabricants de dispositifs médicaux explorent des moyens d’utiliser plus intelligemment l’automatisation pour améliorer la productivité et la flexibilité de fabrication, cette nouvelle génération de systèmes de transport de matériaux peut devenir un outil précieux et relativement facile à mettre en œuvre.
Les fabricants qui ont installé ces types de systèmes de transport ont été en mesure d’améliorer considérablement la productivité et de réduire le temps de cycle. La possibilité de programmer indépendamment chaque palette, en faisant varier sa vitesse et sa direction, offre aux assembleurs et aux fabricants un nouvel outil puissant pour les aider à maintenir leur production rapide et allégée tout en répondant aux besoins de leurs marchés et clients.