Les concepteurs profitent de la transition du métal vers d’autres matériaux. Comment procéder au mieux ?
Il est temps de changer le paradigme du prototypage métallique au-delà du moulage par injection.
La conversion de pièces métalliques en d’autres matériaux crée des économies de poids qui offrent l’une des opportunités les plus importantes pour les industries lourdes comme l’aérospatiale, la défense et le transport lourd. Ces économies de poids sont vitales pour garantir des réductions spectaculaires des émissions de carbone. Et tandis que certains secteurs abordent les problèmes de neutralité carbone avec une fabrication plus efficace et une énergie propre, la plupart des émissions sont générées par l’exploitation, ce qui est résolu en réduisant le poids. En plus d’augmenter les performances, la réduction du poids permet de récupérer rapidement les coûts de conversion, que ce soit par une consommation de carburant réduite, des charges utiles accrues ou une autonomie étendue.
La tradition de fabrication de pièces en métal évolue à mesure que les matériaux avancés tels que les thermoplastiques hautes performances offrent une opportunité de moderniser l’industrie lourde. La nouvelle technologie des matériaux permet d’obtenir des pièces et des composants tout aussi solides et, à bien des égards, meilleurs que les métaux traditionnels, améliorant ainsi les performances et l’efficacité, de la réduction des émissions à la simplification de la maintenance et des réparations. Au lieu de simplement compenser les crédits de carbone, la conversion à partir de métal résout le problème et le fait à un prix abordable, tandis que d’autres options plus respectueuses de l’environnement comme les carburants SAF dans l’aérospatiale restent d’un coût prohibitif. En outre, la conversion réduit non seulement les coûts de carburant, mais également la nécessité de payer pour les crédits carbone.

Il existe des alternatives au travail des métaux.
Les pénuries et l’instabilité des prix qui se sont récemment produites dans les chaînes d’approvisionnement en raison de facteurs mondiaux tels que les interruptions de transport et les tarifs ont également rendu la perspective de conversion à partir de matériaux métalliques plus attrayante, car ils proviennent principalement de l’international. Lorsque le prix et la disponibilité s’avèrent peu fiables, les fabricants doivent examiner comment ils peuvent s’adapter afin que les matériaux qu’ils utilisent soient facilement disponibles et puissent être achetés à un prix abordable. Les matériaux avancés produits localement comme le HX5, un thermoplastique nanocomposite vers lequel la plupart de nos clients se convertissent, sont prévisibles et avantageux pour les chaînes d’approvisionnement et permettent des formes plus complexes mais intenses. Ces composants plus soigneusement pensés peuvent être prototypés, fabriqués et produits en série en quelques semaines par rapport aux mois généralement nécessaires pour les pièces métalliques usinées.
Les ingénieurs réinventent les conceptions
Bien que les matériaux avancés introduisent la promesse d’une disponibilité continue et fiable, ils offrent également aux ingénieurs l’opportunité de réinventer les pièces avec une fabrication et une conception de pointe. Une option importante est en partie la consolidation. Moins de pièces signifie moins de pièces susceptibles de tomber en panne, moins de pièces dans la chaîne d’approvisionnement et moins de pièces à acheter. La consolidation des pièces réduit également les coûts des opérations secondaires – au lieu de plusieurs pièces dans l’assemblage, l’usinage et le revêtement, vous en avez une – tout en réduisant le nombre ou le besoin de composants d’assemblage comme le matériel ou l’adhésif.
Traditionnellement, les concepteurs souhaitant passer du métal ont hésité à rechercher de nouvelles options de matériaux, principalement en raison d’un manque d’expérience ou de compréhension de la façon de prototyper ou de concevoir avec eux. Prenez un client avec qui nous avons travaillé et qui cherchait à alléger un char. Nous avons été appelés pour évaluer la conversion d’une pièce qui pesait 60 livres. Alors que le client pouvait réduire le poids de cette pièce à seulement 30 livres avec HX5, nous avons également aidé à identifier d’autres pièces plus petites qui pourraient économiser du poids supplémentaire. Par exemple, ils ont omis un support de câble qui permettrait d’économiser une demi-livre par pièce, qui a été utilisé plusieurs fois par réservoir et à plusieurs autres endroits sur les plates-formes du client puisqu’il s’agissait d’une pièce commune. L’évaluation des pièces avec une compréhension de ce qui pourrait être fait a créé un plus grand potentiel d’économies de poids collectif que le client n’aurait peut-être pas envisagé autrement.
Grâce à ces recommandations de conception éclairées directement d’une équipe d’ingénierie externe, les équipes de produits internes peuvent améliorer la qualité des produits finis non métalliques et réaliser non seulement des conceptions plus abordables, mais aussi des prototypes supérieurs, même lorsque le moulage par injection est impliqué. Bien que rentables pour la production, les moules à injection ne sont pas efficaces pour le prototypage et ne sont viables qu’une fois la conception finalisée. Fréquemment, les entreprises, soucieuses de leur budget, se contentent alors de prototypes qui ne sont pas représentatifs de ce que sera le produit fini, ce qui est un faux pas particulièrement critique lors de la conversion d’un matériau à un autre, ou d’un processus de fabrication à un autre.
Prototypage
Supposons que vous envisagez de migrer vers une pièce moulée par injection. Dans ce cas, il vous appartient d’avoir un prototype aussi géométriquement équivalent que possible au produit attendu afin que ce que vous testez sur le terrain indique les performances finales. L’étape itérative ici, et l’un des principaux obstacles qui ont existé, est le coût d’un moule d’injection. Un prototype moulé par injection coûte cher, mais le prototypage d’une pièce moulée par injection n’a pas à l’être. Un prototype précis peut être extrudé ou usiné à moindre coût avec la bonne analyse, de sorte que les tests sur le terrain donnent une représentation pomme à pomme – vous permettant de mesurer deux fois et de couper une fois pour une conception de pièce supérieure.
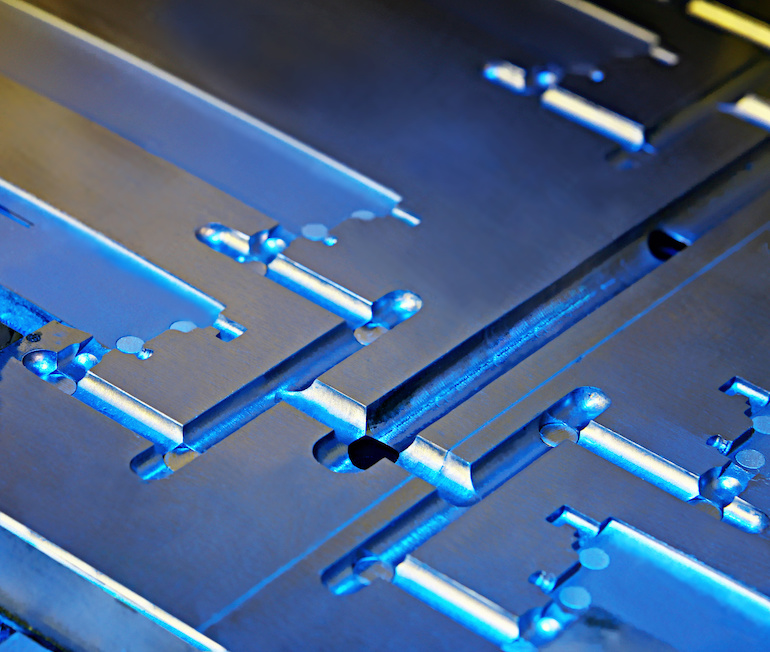
Le noyau d’une matrice de moulage par injection.
De nombreuses équipes de produits internes hésitent ouvertement à poursuivre la conversion des matériaux et le prototypage associé, car elles n’ont pas l’expertise nécessaire pour concevoir avec des matériaux de pointe, un écart sur lequel nous travaillons pour les aider à faire le pont. Une compagnie aéronautique avec laquelle nous travaillons m’a récemment dit : « Nous n’avons tout simplement pas l’expertise interne pour le faire. » Sachant que l’écart existe, nous éduquons les équipes sur la conception pour les non-métalliques tout en les aidant à convertir leurs premières pièces, en leur enseignant les meilleures pratiques et comment répondre à leurs critères de performance. Cela nous permet de leur montrer d’abord le processus et de vérifier leur travail, en supervisant l’analyse afin que lorsqu’ils sont prêts, ils puissent suivre les mêmes étapes dans la conception de futures pièces et composants non métalliques.
L’analyse par éléments finis (FEA) est utilisée depuis des années pour améliorer la conception des pièces en analysant méticuleusement avant la construction, réduisant ainsi le coût du prototypage. Mais, plus récemment, l’optimisation de la topologie de la conception a été utilisée pour améliorer davantage les conceptions en ne mettant le matériel que là où vous en avez besoin. L’optimisation de la topologie de conception est actuellement utilisée pour les pièces usinées et moulées dans les entreprises qui s’efforcent d’atteindre des objectifs de réduction de poids où les géométries sont principalement linéaires mais entraînent des coûts de fabrication plus élevés, en particulier pour les pièces usinées.
Une analyse
Avec des matériaux avancés, l’orientation des fibres est une considération supplémentaire et critique à prendre en compte pour l’optimisation. L’ingénierie de la conception d’un prototype est différente de son analyse. Nous extrayons les données d’orientation des fibres lors de l’analyse du flux de moule, puis les utilisons comme entrée de conception supplémentaire dans la FEA. Ce processus est difficile, prend du temps et de l’expérience. Et parce qu’ils ne sont pas équipés pour l’analyse de l’orientation des fibres, de nombreux concepteurs pèchent par excès de prudence et utilisent un modèle de matériau global plus faible, perdant cette résistance du matériau et la raison pour laquelle ils utilisaient l’optimisation de la topologie en premier lieu.
Cette analyse supplémentaire dans le processus de conception utilise des données brutes et des valeurs hautement caractérisées pour comprendre plus précisément comment une pièce fabriquée avec un matériau de pointe va passer du flux de moule à la FEA. Il faut plus de temps pour créer les géométries complexes requises pour les pièces consolidées, mais cette analyse approfondie aboutit à une conception optimisée des prototypes et des pièces avant la coupe et l’outillage.
Avec la bonne optimisation de la topologie de conception, le bon prototype peut être usiné au lieu d’être moulé, ce qui vous permet de réduire considérablement le temps et les coûts du processus de prototypage. Néanmoins, assurez-vous que la pièce que vous envoyez sur le terrain vous donnera les commentaires réels dont vous avez besoin. Surtout dans les cas où les pièces ont été consolidées, ces prototypes peuvent refléter des conceptions plus intelligentes faites de meilleurs matériaux qui peuvent faire plus et peser moins. La clé est d’avoir la bonne expertise en conception dans le processus. Cette compréhension ne doit pas nécessairement venir d’une équipe produit interne, d’autant plus que la conversion du métal est une nouveauté pour beaucoup. Le prototypage avec des matériaux avancés ne nécessite pas de moules d’injection, juste la bonne conception et l’analyse.
Il est temps de changer de paradigme en matière de prototypage. Un moule à injection n’est pas indispensable pour prototyper une pièce qui sera éventuellement moulée par injection. Au contraire, une optimisation appropriée de la conception des pièces dès le départ permet des prototypes supérieurs et représentatifs sans les dépenses coûteuses d’un moule. L’usinage de prototypes exacts à partir de billettes réduit les coûts, les délais et les incertitudes d’abord dans le processus de prototypage et de conception. En fin de compte, cela compte en introduisant les avantages de pièces plus légères et plus performantes faites de matériaux de pointe. Retarder le coût d’un moule d’injection jusqu’à ce que vous ayez prouvé une pièce sur le terrain crée plus d’assurance que l’investissement en vaudra la peine. Cela signifie également que vous pouvez tester votre conception et obtenir des résultats plus rapidement sans avoir à attendre des semaines pour le moule lui-même.
Alors que nous réinventons la conception des pièces en tenant compte des impacts environnementaux, nous surmontons également les obstacles historiques au travail avec des matériaux avancés qui peuvent alléger un peu notre empreinte.